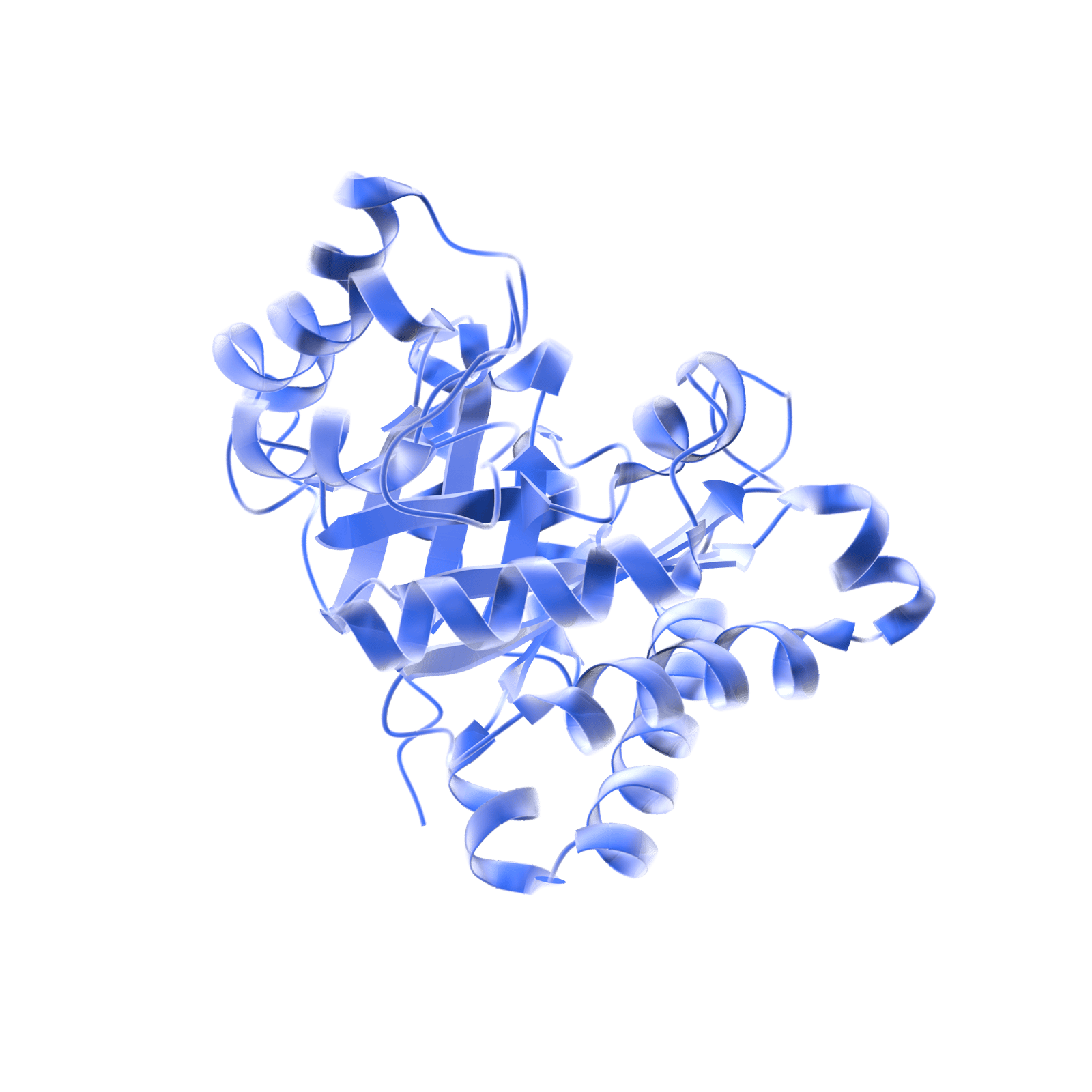
Shear damage to Biopharma products
April 8, 2025 5 min read
Biologically active pharmaceutical ingredients (APIs) consist of molecules with intricate 3D structures that are essential for their function. Differences in the molecular building blocks and biological hosts used for their production contribute to diverse mechanical properties. An API´s sensitivity to stress is affected by these properties, determined by inter-molecular binding forces and molecular structure. In addition to the inherent stress tolerance, the production process, which involves several sequential steps such as fermentation, purification, concentration, formulation, and filling, can increase an API’s exposure to environmental stress. Importantly, as the value of the API rises in the later downstream stages of production, stress-induced product damage can have significant economic consequences. Therefore, when selecting a mixer, it is crucial to consider both the type of API and the specific process step in which the mixer will be used.
During mixing, stress can arise from multiple sources, including mechanical (e.g., baffles, mixer wings, bearings), thermal (e.g., bearings), chemical (e.g., oxidation, pH, salts), inter-facial (e.g., air-liquid and solid-liquid interfaces), and pressure-related stress (e.g., bubble formation, cavitation). Traditionally, bottom-mounted magnetic mixers are commonly used to achieve hermetically sealed vessels and maintain aseptic conditions in API production. A ceramic slide bearing holds the mixer head in place inside the vessel, and a magnetic coupling transfers force from the motor to the mixer head. Importantly, the solution carrying the API act as a lubricant for the mixer head’s slide bearings. As such, two major stress factors to consider when selecting a mixer are heat and shear stress at the bearing site.
Without proper consideration, stress sensitive bio-pharma APIs may suffer from structural degradation, fragmentation, or aggregation (Fig 1) — potentially resulting in loss of function and secondary effects such as filter clogging in downstream processes.
Fig. 1 Stress may cause complex 3D structures to unfold and decay, i.e. fragmentation, consequently leading to product loss-of-function. Fully or partially unfolded or fragmented product may form unspecific interactions causing aggregation, precipitation or entanglement.
In response to these challenges, Metenova introduced Zero-g® technology with a novel vertical slide bearing design with repelling magnets positioned between a top knob on the mixer head and the bearing — removing vertical forces normally placed on a horizontal bearing (Fig 2). As a result, friction and heat generation at the bearing site are reduced, minimizing the risk of bearing failure and lowering the stress imposed on the API.
Fig. 2 Metenova’s Zero-g magnetically coupled mixer. A vertical ceramic slide bearing, represented by the male post, absorbs horizontal forces during mixing. Vertical forces, which are typically managed by a horizontal slide bearing, are in this design counteracted by repelling magnets between the knob, positioned at the top of the mixer head, and male post. Mixer rotation is given by a magnetic drive unit, which transfers torque through the tank plate to the base of the mixer head.
However, despite these improvements in design, highly sensitive APIs still required a more innovative solution. To address this need, Metenova developed Truelev, a bearing-free, fully electronically driven levitating mixer that utilizes magnetism and advanced software to maintain steady-state levitation under applied mixing forces (Fig 3). This maintenance-free design increases the gap between the mixer head and tank plate by a factor of 40, significantly reducing stress-induced damage—an effect supported by both in-house experiments and peer-reviewed studies.
Fig. 3 Metenova’s bearing less Truelev mixer. A software communicates with a control cabinet that levitates the mixer head from the tank plate via the drive unit, rendering the mixer head completely levitating and without contact to the tank plate, contrasting a normal mixer head: male post interaction.
Ultimately, selecting the correct bottom-mounted magnetic mixer requires careful consideration of both the API’s sensitivity to stress and the specific stage of the production process. For highly sensitive products—particularly in downstream applications—a bearing-free magnetic mixer is strongly recommended. Not only does it reduce running costs and minimize maintenance-related downtime, but more importantly, it helps preserve API functionality.
Click here to learn more about the bearing less Truelev mixer.

Andreas Svanström
Andreas Svanström is a Regional Sales & Distribution Partner Manager with an engineering M.Sc. in biotechnology and a Ph.D. in natural sciences, focusing on cell and molecular biology. His previous work includes research in translational and regenerative medicine, as well as roles in associated sales.