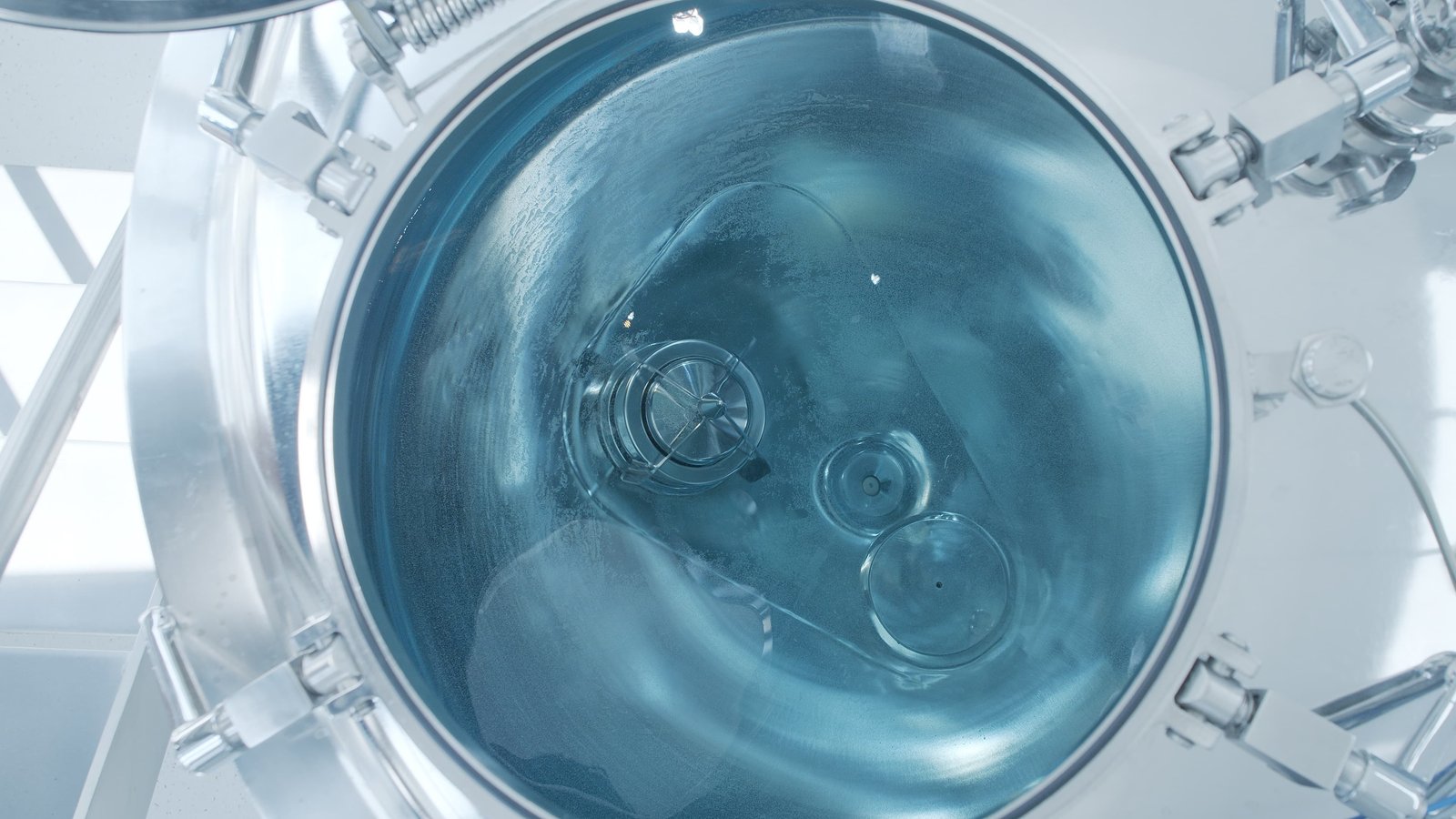
Evaluation services – helping you to navigate in your decision of mixer.
November 13, 2023 6 min read
By predicting a mixing result in advance, it allows you to laborate, make adjustments, and optimize the result before purchasing and installing a mixer. With over four decades of market experience, our team members at Metenova can help you find the perfect solution for you and your project. This is done through the Evaluation Services that we provide. The different services can be combined, or they can be utilized as stand-alone depending on the project’s needs.
Our Evaluation Services – an overview
SELECTION – Our mixer selector is an on-demand digital configurator. By inputting certain parameters such as e.g. vessel dimensions, viscosity, and mixing intensity, you will be presented with a suggested mixer and mixer size suitable for your project.
VERIFICATION – During an application lab test we will be able to verify a process and result, and that the equipment and liquid material behave as intended. Participate either on-site in our lab, on a live digital link, or in a full video afterward – either way, you will be able to see the results for yourself.
SIMULATION – By performing a CFD analysis you will get a digital replica of the intended mixing process, with the correct vessel conditions, material viscosity, etc, and will get a full simulation insight on the performance.
Explaining the evaluation services - and when to apply which service.
Selection - When you want to get a first idea of which mixer you need, and you want to get access to those particular data sheets, this is a great tool to use. After completing the configurator, our mixing specialists and sales representatives are available to discuss any questions with.
Verification - This type of test can serve as verification that a mixer will work satisfactorily in the real application. Even if the scale is smaller, it can still give valuable insight into the mixing and the whole process. Potential issues can be observed that might not be directly related to mixing performance, e.g., foaming, lump formation etc. Vessel sizes from a few liters up to 1000 liters are available at the Metenova Application Lab. Therefore, the tests can range from lab to pilot/production scale size. Vessel sizes up to 600 L (I.D 800 mm) have transparent walls. It gives unique possibilities to follow the mixing behavior in the whole fluid, all the way from the top to the bottom of the vessel.
Simulation – CFD is a powerful tool especially when new and complex vessel designs are considered. It provides valuable insight into the fluid’s velocity field, potential stagnant zones, mix times, etc. Different equipment designs can be evaluated in an early stage of the project. This can minimize the risk of potential surprises later on.
The complexity of the simulation will vary depending on the mixing scenario. Simulation of vortex formation or a two-phase system is much more demanding compared to a single-phase system with a flat top surface.
Theoretical skills and experience from CFD simulations are of course essential for a successful simulation. Planning is also key to success. The desired objectives and the constraints must be agreed upon and the time needed for this is often underestimated.
When the examined process contains a lot of uncertainties it will be hard to know the validity of the simulation. Especially in those cases, it is important to verify the quality of the simulation with lab tests too.
To sum it up, CFD is a powerful tool to evaluate mixing behaviour but not without some effort. If possible, it is advisable to verify the CFD model with lab trials.
Customer success story: Avoiding costly redesigns of vessels during the transition into multi-purpose production.
Background and the challenge
A client needed to confirm the design of a vessel was working properly before the vessel could be approved for installation in a new plant. The scope of the project changed after the construction of the vessel had started. Therefore, it first had to be proven that the design could handle all critical process steps such as:
- Was the intended vessel design suitable for the preparation of solutions of an amino acid powder?
- How would different filling levels in the vessel influence the mixing result?
The solution – performing an Application Lab Test.
An Application Lab test was performed in Metenovas facilities, where the customer attended, but also received a written report and film of the lab test afterward. A model of the intended vessel was built in the lab with the correct geometries, and the correct raw material was used during the tests. The test was successful and resulted in the vessel design getting approved for the new project scope, without the need for a costly and time-consuming redesign. The lab result could also help minimize the risks regarding uncertainties with the process performance. From initiation to the final lab result, the timeframe was 6 weeks.

Johan Nordberg
Johan Nordberg, Application Lab Engineer at Metenova with 20+ years of expertise from various roles in the chemical industry is responsible for the digital lab at Metenova.