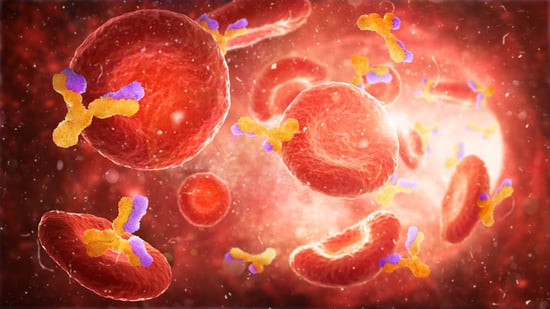
Low shear applications
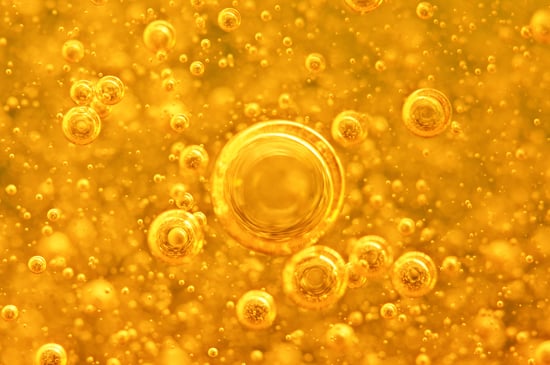
Emulsification and high shear applications
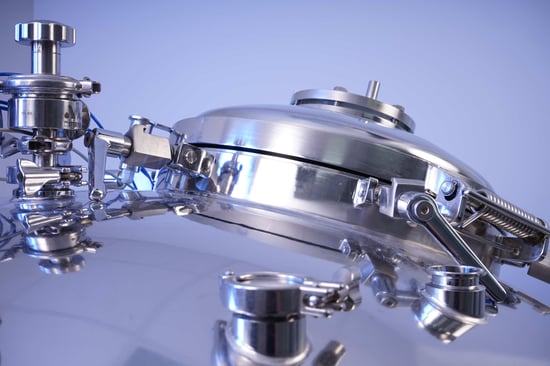
General mixing applications
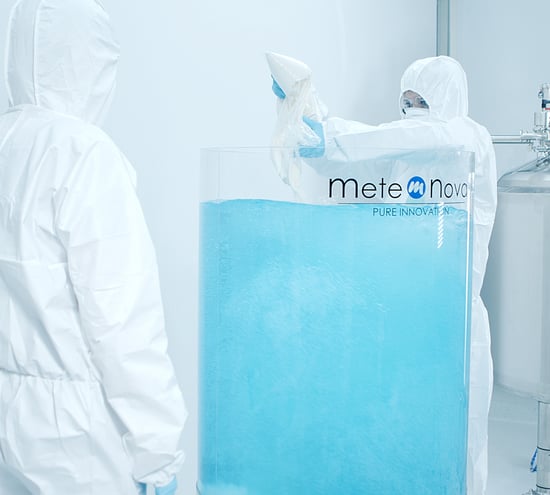
Powder and vigorous applications
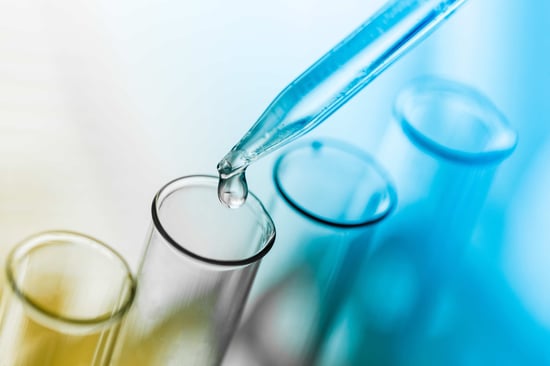
Metenova mixers give you the perfect result every time. No matter which application area, we have the mixer for your needs.
Some components of pharmaceuticals, such as proteins, cells, or final fill solutions, are especially sensitive to shear stress. When mixing such products, it is a delicate balance between mixing enough to ensure homogeneity of the mixture and gently to protect the shear-sensitive product from damage.
As these products are being purified and concentrated their value and shear sensitivity increase.
Protein chains that are exposed to too much shear will break and form agglomerate, which can be indicated through clogged filters or failing product quality.
Ensuring compliance of the mixing operation and best product recovery are key factors for success.
To facilitate this, we developed a fully levitating bearing-less technology with a high-efficiency design that allows the shear-sensitive product to mix homogeneously without the risk of being damaged.
The emulsification of non-soluble liquids is a challenge by default. Doing this in a pharmaceutical production environment requires a vessel design and mixing system appropriately optimized for this particular purpose. An example of such an application could be water and oil-based emulsion products used for creating an oil film for tablet coating.
High shear is also used to quickly get rid of “lumps”, and “fisheyes” or simply implement particle size reduction.
Often the two applications are performed by utilizing a rotor/stator design and with high energy input.
In a pharmaceutical plant, many mixing applications are more general, yet still critical from an aseptic and performance point of view. These applications can be anything from heat transfer, keeping suspensions homogeneous, or liquid-to-liquid mixing. Ensuring mass heat and gas transfer is of importance as well as the ability to create scalability of mixing performance as vessel volumes change in the different process steps and applications. Efficiency in mixing performance is driven by optimizing the vessel design, mixer location, mixer design, and operation with the desired application. Essential to achieving good performance is the efficiency of the mixer design itself, promoting fast mixing times increasing the efficiency of the facility, or reducing the risk of shear impact by running the mixer at reduced speed creating gentle but adequate mixing.
General mixing applications like these require a multi-versatile mixer that can address several different needs.
The biggest challenge working with powders - is working with powders.
Some powders are low-density and have a hydrophobic character, which leads them to float on top of the liquid in the vessel. Other powders are high density and still have a hydrophobic character, which leads them to sink into the liquid in the form of large lumps, not being wet.
In some applications, a powerful vortex is needed that pulls down the powder to the mixer at the bottom, which allows for a homogeneous mixture.
When aiming to achieve a vortex, it is very important to consider the vessel design and its geometrics, the position of the mixer, and the mixer output. If a vessel is wrongly designed, it may be impossible to create a vortex inside.
In applications where the liquid is very aggressive, such as strong acids or bases, stainless steel is sometimes not suitable. By replacing the stainless steel with polypropylene (PP) you will allow for the application to run in a more cost-efficient, yet product-safe, manner.